Electroform Stencil
BlueRing Stencils manufactures electroformed nickel stencils to offer superior paste release as industry standard board designs demand smaller apertures and pitch. Electroformed stencil aperture walls are smooth (mirror-like), providing less surface area for solder paste to cling to. Instead of laser cutting apertures, nickel is formed around a photo resist template of apertures that matches board designs. Electroforming also allows quick turnaround times for jobs with large aperture counts.
Advantages of Electroform Stencils:
- Quick Turnaround: Ideal for jobs with a large aperture count, ensuring fast production times.
- Smooth Aperture Walls: Enhanced paste release due to the smoothness of the aperture walls.
- Higher Paste Transfer Efficiency: Electroform foils outperform uncoated laser-cut stencils in paste transfer efficiency.
- Superior Paste Release: Nickel-formed foils, when laser cut, provide better paste release compared to laser-cut stainless steel foils.
- Enhanced Strength and Hardness: Electroform stencils boast higher tensile strength and hardness than stainless steel stencils.
- Custom Thicknesses: Electroformed foils can be produced in non-standard thicknesses to meet specific requirements.
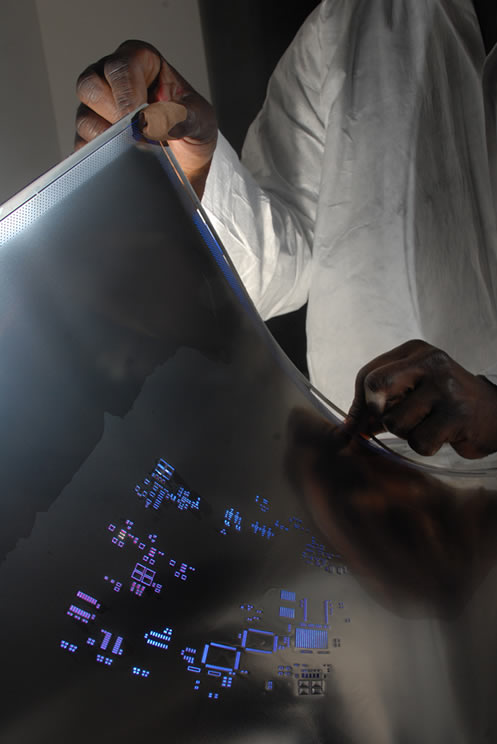
Specifications
Foil Thickness: | 1mil – 7mil |
Aperture Tolerance: | ± 0.3 mil |
Thickness Tolerance Over Area: | ± 0.4 mil over 10” |
Center to Center Aperture Tolerance: | 10×10” area: within 0.001” of original 16×16”: 0.0015” 20×20”: 0.002” |
Trapezoidal Aperture Walls: | Taper is approx. 0.1 mils (0.0001”) per side per mil of foil thickness. (e.g. 5 mils thick foil would have ~ 0.5 mils taper per side) |
How does electroforming work?
1) Resist on mandrel is imaged with a master photoplot.
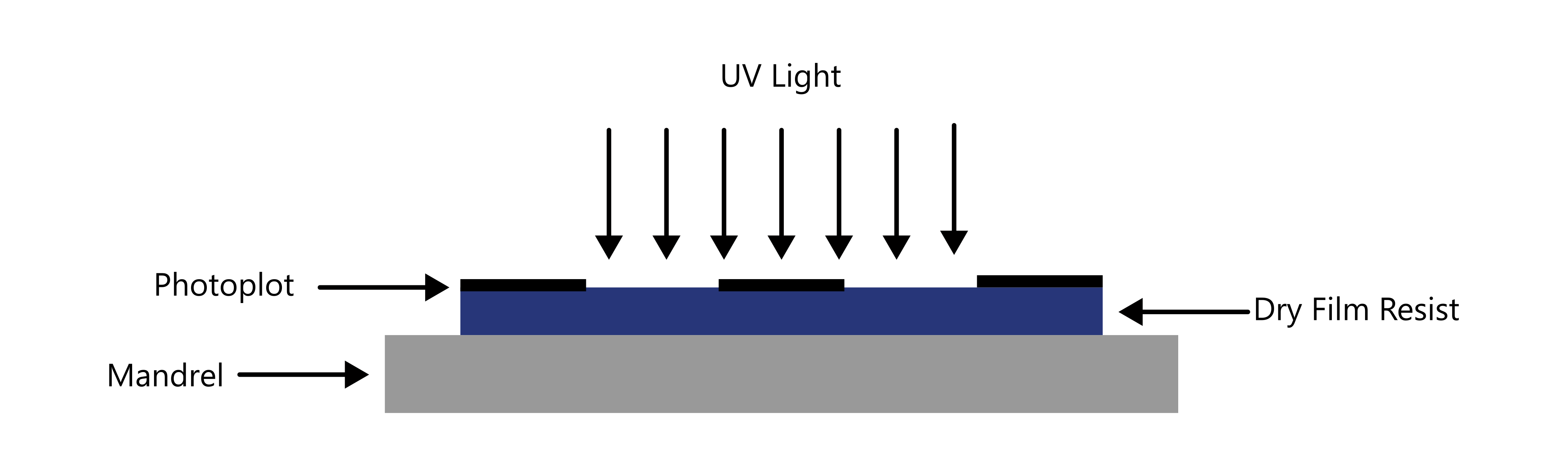
2) Undeveloped resist is stripped off, leaving pillars of developed resist.

3) Once immersed in the nickel bath, the nickel atoms follow the electrical current and are deposited onto the mandrel.

4) After removing from the mandrel and remaining resist, you are left with a nickel stencil.
